How Thinner Laminations Improve Power and Performance in High Speed Motors
| 3 min read
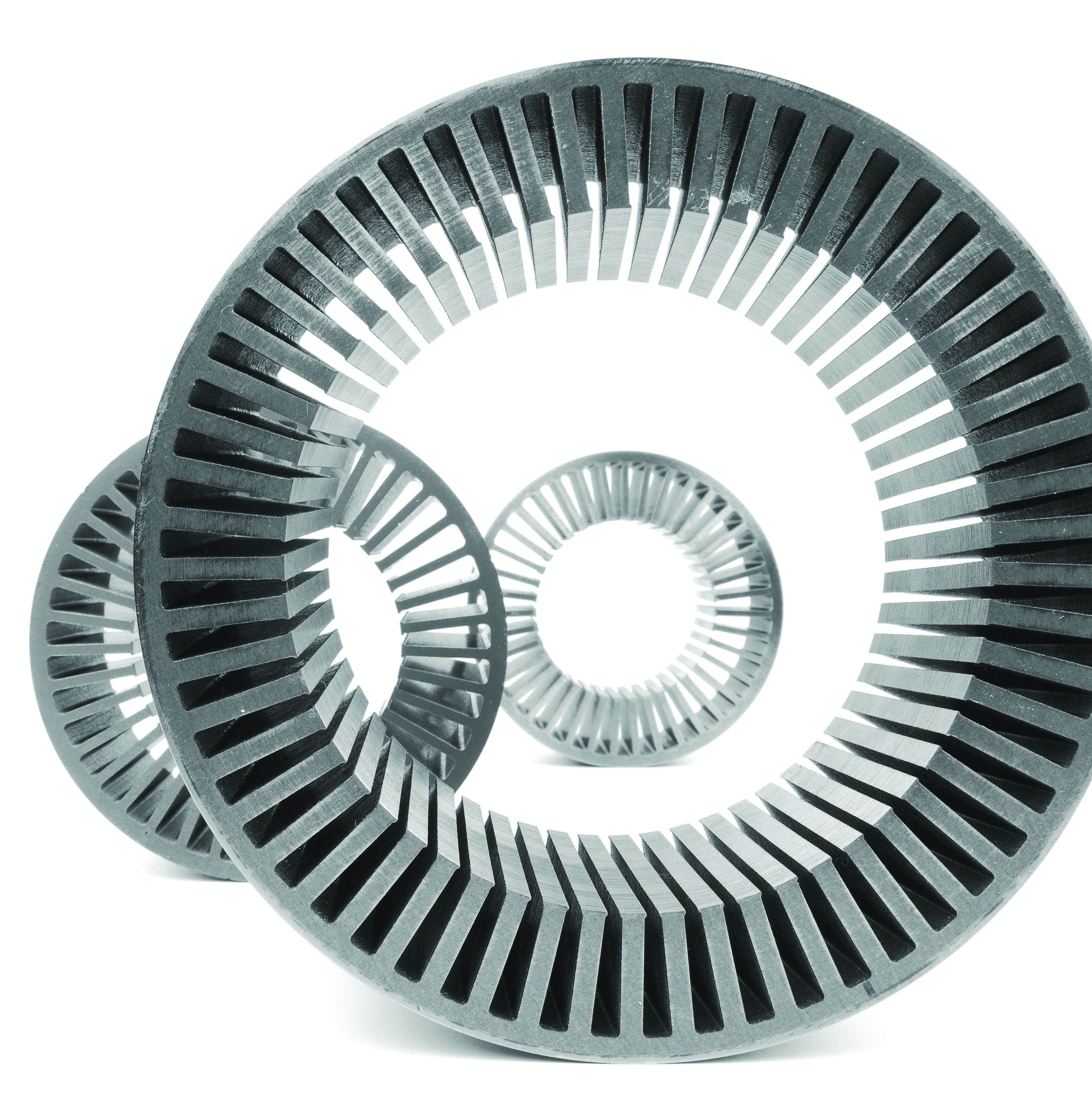
Enhanced power density and torque density are critical for high-performance motors. E-mobility vehicle designers must carefully consider weight and packaging constraints for their impact on operation. Recent advancements in electrification sectors such as EVs, hybrid and electric aircraft, drones, defense vehicles, and medical devices further highlight the need for improved system performance.
The emergence of SiC and GaN power electronics is expanding the options for powertrain designs. New motor drives using these technologies are extremely efficient at high frequencies, enabling significantly higher power density. The higher switching frequencies have a negative effect on stator and rotor performance, but these effects can be mitigated through proper material selection and stack construction.
For high-speed motor applications, thinner soft magnetic laminations in stator and rotor stacks help achieve higher continuous motor power because the lamination materials exhibit lower core losses due to lower eddy current contributions.
As motor speed increases, it becomes critical to choose the best combination of alloy and lamination thicknesses to keep iron losses low and achieve the highest possible continuous power density, along with high torque responses.
Material and design
Choosing the right material, thickness, and stack combination is key for optimizing motor or generator output. A range of high-performance soft magnetic alloys with the highest induction, high permeability, and low core losses are available. Once the optimal material is determined, the designer should then determine the optimal thickness. Most alloys are available in a selection of standard thicknesses to support various frequencies, and thicknesses can be customized for specific applications.
The table below provides core loss data for popular soft magnetic alloys at different frequencies and material thicknesses. Core losses increase with higher frequency but are lower when lamination thickness is reduced.
CORE LOSS AT VARYING FREQUENCIES AND MATERIAL THICKNESSES
Optimizing lamination thickness
The figure below can be used as a guide to the optimal lamination thickness for specific application frequencies. It shows a representative hysteresis and eddy current loss response breakdown for different Hiperco® 50 lamination thicknesses.
As operational frequency increases, thinner laminations become more effective due to the decrease in eddy contributions, even though the hysteresis losses increase.
HYSTERESIS AND EDDY CURRENT LOSS AT VARYING FREQUENCIES AND MATERIAL THICKNESSES
The crossover point where eddy current losses dominate overall losses is a useful guide. At frequencies above this crossover point, motors often experience adverse effects that impact performance. It’s important to choose the appropriate material thickness to stay below this crossover point for the motor operational frequency.
As a starting point, 0.15 mm Hiperco laminations perform well from 300 to 800 Hz. From 800 to 1800 Hz, 0.10 mm material performs better. At frequencies above 1800 Hz, even thinner laminations are recommended. Again, this is only a starting point — additional considerations are important when optimizing your stator and rotor stacks for high frequency.
Optimizing material properties
The magnetic and mechanical properties of alloys such as Hiperco 50 can be modified by varying process parameters to improve core loss behavior. Through expert processing, we can modify the range of optimal operational frequency for a lamination thickness. This is particularly important, as using thin laminations when not necessary drives up the cost of stator and rotor stacks, often without much improvement in performance.
The optimal approach and material properties are a function of the motor design and application. These choices are particularly critical for motors operating at high frequencies.
Carpenter Electrification’s application experts can help you select the best alloy grade, mechanical and magnetic properties, lamination thickness, and stack processing approach for your high-speed motor.
WE’RE HERE TO ADVANCE YOUR PERFORMANCE. Contact us today.