How Iron-Cobalt Alloys Create Power-Dense, Zero-Emission Trucks
| 14 min read
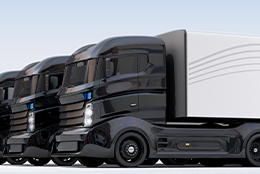
Electrification of passenger vehicles is becoming a reality. Battery prices have dropped from $1100/kWh in 2010 to $156/kWh, with the numbers of electric vehicles being sold expected to increase from 2.5 to 31 million by 2030. Similar to the benefits of EVs to consumers, the electrification of transport trucks would enable lower maintenance, better efficiency, and lower the ownership cost of transporting a payload, not to mention the substantial environmental effects of zero-emission trucks. A recent study by the Union of Concerned Scientists (UCS) reported that the electrification of trucks would lead to a 44-72% reduction of eCO2 emissions. Government regulations are also moving the needle on the adoption of electric trucks, as 15 U.S. states and Washington D.C. announced in July 2020 that they would develop a plan for 100% of all new medium- and heavy-duty vehicles sold be zero-emission by 2050, with an interim target of 30% zero-emission vehicle sales by 2030.
Thus, the electrification of transport trucks is not a matter of if, but when. With federal and state governments increasing incentives and the opportunities to reduce the cost of ownership, fleet owners and large OEMs are moving forward with electrification initiatives. Despite remaining practical challenges such as not having enough power density of the battery modules, infrequent charging networks, long charging wait times, and the lack of an ecosystem to manage electric trucks, OEMs continue to announce new models of electric trucks. Multiple OEMs had announced Class 7 and 8 truck launch in 2021 alone, although additional challenges presented by COVID-19 may alter these timelines.
One significant challenge to the expansion of electric trucks is the lack of sufficient energy density in the battery modules. OEMs have announced trucks with a range of 300 miles, or in the maximum case 500 miles, based on current battery technology. A diesel truck travels on average 600-700 miles a day, meaning electric trucks fall short by ~50% of the range needs. This is a hard gap to fill with the incumbent battery technology. There are ongoing efforts by OEMs, Tier-1s, and multiple small startups to innovate a high-energy-density battery at a reasonable cost. For example, Tesla recently announced the ability to double battery density and half per kWh cost simultaneously within the next 3-5 years. A startup called Quantumscape developed a >400 Wh/kg energy-dense battery, which is roughly one and half times better than other state-of-the-art solutions, but this comes at a steep price.
Carpenter Technology is investigating complementary solutions to provide a unique motor technology option to work as an auxiliary force and increase the range of electric trucks. We ran a case study and found that electric motor technology based on a stator made of the soft magnetic iron cobalt alloy Hiperco® can increase electric trucks' range 8-10%. A 300-mile range electric truck can travel an additional 30 miles without any extra battery load.
Hiperco alloy motor technology is well known in the aerospace market, where Hiperco stator cores are used in over two-thirds of the auxiliary power units (APU) used to generate power to kick-off the main engine in commercial airplanes. A Hiperco stator core increases the motor's torque, power density, and efficiency while reducing the cooling requirement. The advanced iron cobalt alloy performs with 20-25% higher magnetic induction relative to incumbent electrical steel/Si-steel. A permanent magnet motor modeling showed an 18% increase in the peak torque and a 52% increase in continuous power. Increased torque would make electric trucks more agile by increasing acceleration and speed, while the increase in continuous power is useful for improving the drive cycle efficiency. Furthermore, the motors run cooler than other technologies. Thus, utilization of Hiperco will enable a ~10% more energy efficient truck with an opportunity to run the motor with reduced thermal management.
While the raw material cost of Hiperco is higher than the presently used Si-steel, integrated Hiperco motor technology reduces costs for electric truck manufacturers and fleet operators. Manufacturers with more powerful Hiperco motors can save 10% on battery weight and cost while maintaining their vehicles' range. This translates to about 1000 lbs of battery weight savings in addition to about in $4000 powertrain cost savings for a battery pack with double the power density at $75/kWh. Fleet operators can expect two added benefits to using Hiperco motor technology. For the overall service life of a truck, estimated at 1.5 million miles, the 10% battery size reduction saves approximately 10% of the electrical expenses of charging, estimated in the range of $33,000. Furthermore, the battery weight savings help to increase payload capacity by about 2%, beneficial to 50% of the heavy-duty class 8 trucks operating in the total weight range of 60,000 – 80,000lbs. The anticipated profit increase for fleet operators would be in the $22,000 range during the lifespan of a truck.
In summary, despite the increased material costs of Hiperco, electric truck motors utilizing this technology offer cost benefits of around $59,000 for EV truck manufacturers and fleet operators throughout the truck's service life, opening the door to further adoption and ever-advancing innovation in the future of electric mobility. Want to learn more about electric vehicle solutions?