How Soft Magnetic Alloys Improve Performance for Electric Motors
| 2 min read
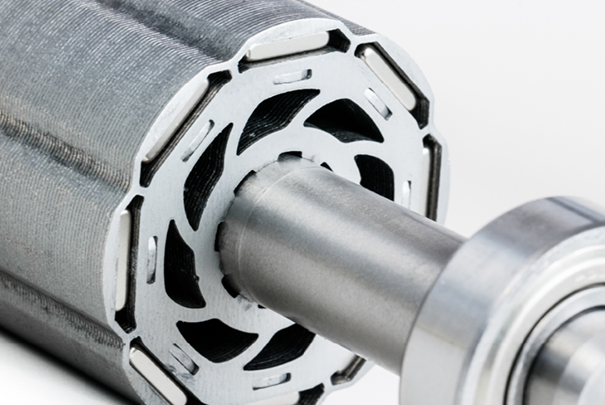
Next-generation iron-cobalt alloys and novel process technologies drive peak stack performance for power- and torque-dense e-motors
Motor designers for e-mobility (electric vehicles, hybrid and electric aircraft) and drones are increasingly turning to iron-cobalt stator and rotor stacks for higher performance.
Carpenter Technology’s advanced iron-cobalt soft magnetic alloys (Hiperco Family) provide maximum magnetic output for power- and torque-dense motors and generators. The company has spent more than half of its 130 years of existence perfecting the processing of soft magnetic materials with the highest induction, permeability, and lowest core losses. Power density improvements of 20 to 30 percent have been achieved, opening the door for e-motor designers to create motors that are 20 to 30 percent smaller, have 15 to 25 percent higher torque, and have up to 3 percent greater motor efficiency.
To serve customers from design to prototyping to mass production and realize improved motor responses using these high-performance alloys, Carpenter Electrification expanded this expertise into the production of stator and rotor stacks.
Expertise matters: The same iron-cobalt alloy characteristics that deliver high magnetic performance also present challenges when producing stacks. Improper processing can compromise rotor and stator performance by as much as 50 percent. Each process step, including lamination cutting, insulation, bonding, and machining, adversely affects magnetic performance of the alloys. Without data-driven knowledge and an optimized approach, lamination stack processing can result in rotors and stators that perform only marginally better than standard electrical steel.
Lamination thickness is also critical to peak stack performance. Too thick, and eddy current loss increases. Too thin, and more processing is required, which increases manufacturing costs. Finding the optimal lamination thickness changes from application to application, as different e-mobility vehicles have different motor needs.
Carpenter Electrification engineers have a deep understanding of metallurgical structure-magnetic property relationships and have developed processes to isolate and eliminate these detrimental variables. Their alloys and stacking methods for low growth, high strength, and tailored properties support the most demanding motor design requirements and production tolerances — ultimately resulting in superior motor responses.
A variety of processing technologies, including booklet EDM, laser cutting, and notch and progressive die stamping are available and tailored based on an application’s overall requirements. Stamping, for example, offers the lowest high-volume cost and highest magnetic performance for mass production, but sacrifices tolerance control because iron-cobalt alloys experience growth during processing. So Carpenter Electrification developed capabilities to understand and predict the growth of a lamination, allowing the company to produce first article stacks with tight tolerances via stamping. Without having to waste additional time and expense on die design iterations, e-motor manufacturers can move quickly through prototyping to mass production.
Carpenter Technology’s portfolio of high performance soft magnetic materials are available in lamination thicknesses from 0.05 to 0.5 mm and are backed by aerospace and automotive quality certifications. The company supplies more than 5 million laminations every year and is the leading supplier of iron-cobalt alloys for the generators and APUs used on all commercial and military aircraft. Carpenter Electrification works with e-motor designers to create best-in-industry processes and solutions. Together, the sister companies are a one-stop-shop for producing top-performing stator laminations, rotor laminations, and stacks for current applications while validating advanced processes for next-generation stacks.