Maximizing eVTOL Motor Performance: From Materials to Manufacturing
| 10 min read
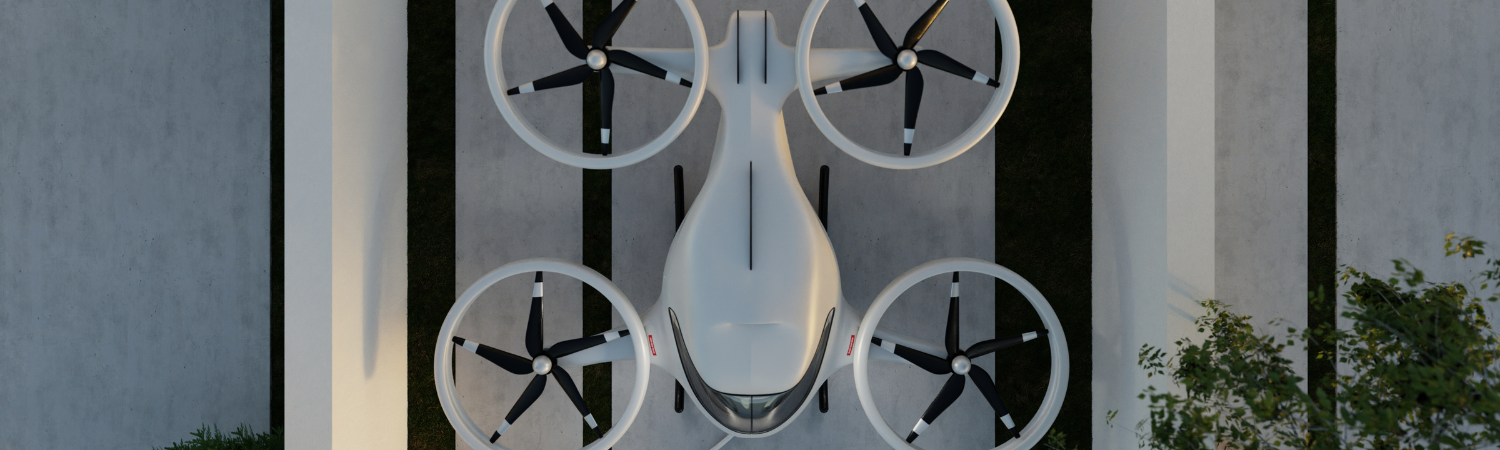
Electric Vertical Takeoff and Landing (eVTOL) aircraft are revolutionizing urban transportation, promising to transform everything from emergency medical services to daily commuting. These innovative aircraft combine vertical mobility with quieter operation, reduced emissions, and lower operating costs.
With major airlines investing heavily in air taxis to help commuters navigate crowded city skies, manufacturers face an unprecedented challenge: developing motors that deliver exceptional performance while meeting rigorous aerospace standards.
Understanding eVTOL Motor Requirements
Every gram impacts performance in aircraft design. Modern eVTOL platforms must integrate cutting-edge avionics, structural components, batteries, and propulsion technologies to achieve optimal performance. The motor and electric propulsion unit (EPU) critically influences multiple parameters, including takeoff weight, payload capacity, cruise speed, range, hover time, and flight time.
The four primary eVTOL architectures each present unique propulsion challenges. Tilt-rotor systems must maintain consistent performance through orientation changes, while lift+cruise configurations require specialized motor systems for distinct flight phases. Multi-rotor designs demand perfect synchronization across multiple units, and vectored fan architectures need precise power modulation.
These aircraft serve diverse purposes, from air taxis for short-range urban travel to logistics, emergency response, sightseeing tours, and personal recreation. These varied requirements have pushed the industry beyond traditional solutions, particularly regarding material selection and manufacturing precision.
The Critical Role of High-Torque Motors
The industry's early reliance on silicon steel-based interior permanent magnet (IPM) motors from the electric vehicle sector revealed significant limitations in aerospace applications. While these motors proved economical and reliable for ground vehicles, they imposed unacceptable performance trade-offs in aircraft use. The debate between higher-power and smaller motors has largely been settled in favor of high-torque solutions, driven by their superior ability to deliver enhanced lift, thrust, and payload capacity.
The implementation of high-torque motors transforms aircraft capabilities in several critical ways:
- Range Enhancement: Motors with higher power extend flight range by 12-20% while enabling higher cruise speeds
- Payload Capacity: A 20% increase in payload capacity (90-135kg) enables an additional passenger per flight
- Economic Impact: This additional passenger capacity can generate up to $1.1 million in annual revenue per aircraft
- Energy Efficiency: Enhanced torque density improves propulsion efficiency by up to 3%, critical for battery-powered flight
- Operational Flexibility: Improved acceleration and thrust control enable more precise flight operations
- Size Optimization: Advanced motor designs achieve 20-30% size reduction while delivering 15-25% higher torque
Engineering Motor Excellence
The heart of motor performance lies in the sophisticated interaction between stator and rotor components. As the motor's largest magnetic component, the stator demands precise engineering to generate the rotating magnetic fields essential for motor operation. Its frame supports the core and protects the three-phase winding, while thin stacked laminations wound with insulated wire create the magnetic field patterns necessary for optimal performance.
The rotor faces unique challenges. Massive centrifugal forces demand exceptional mechanical stability. The interaction between windings and magnetic fields produces torque around the rotor's axis, which is coupled to the propeller either directly or via a geared system, requiring a careful balance between magnetic properties and mechanical resilience.
Key design considerations for both components include:
- Design Evolution: Moving beyond traditional tethered applications like fans and appliances into the demanding realm of autonomous flight.
- Operational Demands: Adapting motor design for varied use cases from short urban hops to extended cargo missions.
- Power Management: Balancing peak performance with sustainable operation across diverse flight conditions.
- Voltage Management: Stator windings require heavy insulation for high-induced voltages.
- Current Distribution: Larger stator windings handle heavy currents for primary motor function.
- Magnetic Optimization: Stators maximize magnetic properties for field generation, while rotors balance magnetic and mechanical performance
- Thermal Control: High-frequency operation necessitates low core loss materials and components and may require sophisticated heat management systems.
- Dimensional Precision: Maintaining critical tolerances down to 0.002 inches for optimal gap performance compared to a legacy aerospace APU standard of 0.008 inches.
- Stack Integration: Ensuring perfect alignment and assembly for maximum electromagnetic efficiency
- Material Selection: Choosing optimal materials for each component based on its specific operational demands
Material Innovation Through Carpenter Electrification's Hiperco® 50
Our Hiperco® 50 alloy stands apart through several key advantages. Its higher magnetic permeability and superior induction capabilities provide the foundation for more efficient energy conversion. The material's unique chemistry, tailored for low core loss and high strength, enables unprecedented power density in a compact format.
This specialized material and processing expertise ensures the highest-performance stator and rotor stacks through a combination of optimal design, processing, and construction techniques. When incorporated into motor design, these properties enable:
- 25% greater torque density for improved flight performance
- 30% improvement in power density while maintaining reliability
- Size reduction of up to 30% compared to traditional motors
- Enhanced thermal characteristics for cooler operation
- Extended motor lifespan through improved material stability
- Superior dimensional control and high-strength properties
- Tailored magnetic properties for demanding aerospace requirements
Manufacturing Excellence at Scale
Traditional manufacturing methods struggled with several critical limitations that compromised motor performance. During heat treatment, iron-cobalt materials underwent dimensional changes, leading to distortions. Achieving necessary tolerances required expensive post-processing through EDM machining, while imprecise stacking methods resulted in lower copper fill factors that compromised motor power output. Additionally, high-precision methods like EDM cutting proved prohibitively slow for high-volume production, creating a bottleneck in manufacturing capacity.
Carpenter Electrification has revolutionized this process through our integrated manufacturing approach. Our state-of-the-art capabilities at each production stage enable us to deliver high-performance components consistently. Our advanced production process incorporates:
- Precision strip hot rolling with controlled dimensional stability
- Controlled strip processing with highly repeatable results
- Sophisticated heat treating and bonding processes that minimize material distortion
- New automated stacking methods in controlled environments for optimal assembly and repeatability
- Advanced lamination techniques ensure consistent magnetic performance
- Comprehensive testing protocols at every production stage
- Specialized assembly processes for improved stack productivity
- Advanced magnetic performance verification systems
Quality Assurance in Volume Production
Maintaining aerospace-grade quality in high-volume production requires comprehensive quality control measures. Our integrated approach begins with material validation and extends through final assembly, ensuring every component meets rigorous aerospace standards.
Our focus on soft magnetic stator and rotor laminated stacks with high induction, high permeability, and low loss materials combines with expert processing methodologies to unleash maximum performance benefits. Advanced magnetic performance testing verifies that each stack achieves optimal performance, while automated inspection systems maintain quality across production runs.
This stringent quality control system incorporates the following:
- Real-time dimensional monitoring for precise tolerance control
- Advanced magnetic performance verification
- Statistical process control implementation
- Complete production traceability
- Automated inspection systems for consistent quality assessment
- Comprehensive material property validation
- Specialized testing for both magnetic and mechanical properties
- Environmental controls during critical manufacturing stages
Additionally, we are AS9100 certified, meaning we meet and exceed the rigorous standards set for aerospace applications, ensuring that our products are top-notch and consistent in quality.
Future Perspectives and Innovation
The evolution of eVTOL motor technology continues to accelerate, with Carpenter Electrification leading development in several key areas. This progression marks a significant leap from traditional electric motor applications in stationary devices to the demanding requirements of autonomous flight systems. Our ongoing research focuses on advancing thermal management, increasing productivity, improving stack mechanical strength, and optimizing stator-rotor gap dimensions.
Key areas of development include:
- Advanced cooling solutions for high-frequency operation
- Novel winding configurations for improved power density
- Dimensional control for tighter tolerances and improved motor operation
- Innovative stack assembly techniques for high precision and enhanced reliability
- Optimized processing for maximum efficiency and enhanced mechanical properties
These innovations build upon our established expertise in materials science and manufacturing excellence.
Advancing Urban Air Mobility
The transition from traditional electric motors to eVTOL applications represents more than just an evolution in technology — it marks a fundamental shift in how we approach urban transportation. Unlike conventional tethered electric motors found in everyday appliances, eVTOL motors must deliver exceptional performance while meeting the stringent safety and reliability requirements of aerospace applications. The future of urban air mobility depends on continuous advancement in motor technology.
Integrating advanced materials, precision manufacturing, and rigorous quality control becomes increasingly crucial as the industry moves toward widespread commercial deployment. Carpenter Electrification's comprehensive approach provides the foundation for next-generation aerospace motors, enabling the transformation of urban transportation.
Ready to optimize your eVTOL motor performance? Contact Carpenter Electrification to explore how our expertise in materials and manufacturing can elevate your electric propulsion systems to new heights.