Optimized Assembly and Bonding for High-Performance Hiperco® Stators and Rotors
| 8 min read
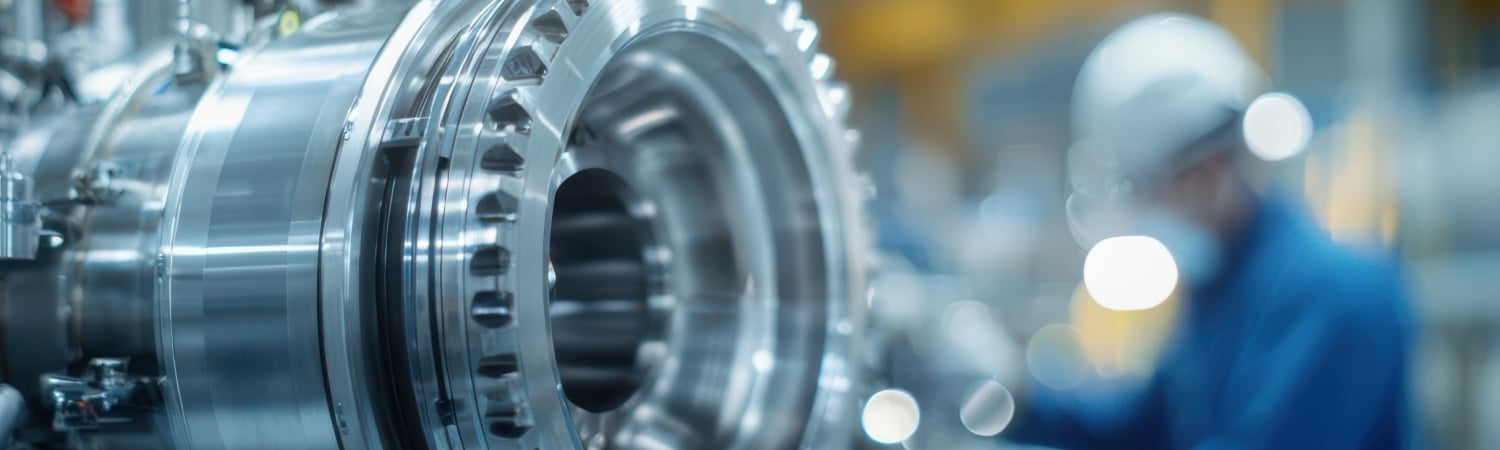
With industries like eVTOLs and electric airplanes pushing the boundaries of performance, the demand for high-performance electric motor components — especially stator and rotor assemblies — has never been greater.
At Carpenter Electrification, we're at the forefront of this revolution, offering optimized assembly and bonding techniques for Hiperco® stators and rotors that set new standards in precision manufacturing. Let's explore this in more detail.
Why Stator and Rotor Assembly Matters for High-Performance Motors
The heart of any electric motor lies in its stator and rotor assembly. These components are fundamental to generating the electromagnetic fields that produce motion, and their design and construction directly impact a motor's efficiency, power output, and longevity. The stakes are even higher in high-demand industries such as eVTOL (electric vertical take-off and landing), electric vehicles, and high-precision manufacturing equipment.
Hiperco® alloys, known for their superior magnetic properties, have emerged as a game-changer in electrification. However, precision in assembly and bonding is crucial to fully harnessing the potential of Hiperco® stators and rotors. This is where Carpenter Electrification's expertise comes into play, offering solutions that maximize performance and address the unique challenges manufacturers face in these cutting-edge sectors.
Understanding Stators vs. Rotors: Core Functions and Key Differences
Understanding the core functions and key differences between stators and rotors is crucial to appreciating their role in high-performance motors. Take a look.
Stators: The Stationary Powerhouse
- Definition: The stator is the stationary part of an electric motor.
- Components: It consists of a frame, winding, and a static core made of thin, stacked laminations.
- Function: Generates a rotating magnetic field that interacts with the rotor to produce motion.
- Key Requirements: High permeability, high induction, and low losses are critical for optimal performance.
Rotors: The Dynamic Core
- Definition: The rotor is the rotating section of the electric motor.
- Components: It consists of a core of soft magnetic laminated stacks, often with interior or exterior mounted permanent magnets, attached to a shaft to power motion.
- Function: Interacts with the stator's magnetic field to produce torque and rotation.
- Key Requirements: Magnetic properties must be balanced with robust mechanical performance to withstand high rotational speeds.
The Challenges of Stator and Rotor Manufacturing
Manufacturing high-performance stators and rotors presents unique challenges that require innovative solutions. These challenges stem from the complex interplay between material properties, design requirements, and production processes.
As the demand for more efficient and powerful electric motors grows, manufacturers must navigate these obstacles to deliver components that meet increasingly stringent performance criteria. Let's explore the critical challenges in detail:
- Precision Assembly: Ensuring stacks are bonded without defects is crucial for optimal performance.
- Scalable Production: Maintaining quality while scaling up production to meet market demands.
- Material Durability: Preventing long-term wear to ensure consistent performance over the motor's lifespan.
- Balancing Properties: Optimizing both magnetic and mechanical properties, especially in high-speed applications.
Carpenter Electrification's optimized assembly and bonding techniques using Hiperco® alloys directly address these challenges, providing solutions that enhance efficiency and performance across various applications.
The Role of Hiperco® in High-Performance Motor Applications
These advanced alloys have become increasingly crucial in industries where power density, efficiency, and reliability are paramount. Understanding the unique characteristics of Hiperco® alloys is vital to appreciating their impact on motor design and performance. These characteristics include:
- High Magnetic Saturation: Hiperco®’s high magnetic saturation allows for stronger magnetic fields, enabling motors to generate more power without increasing in size — a critical advantage in space- and weight-sensitive applications like eVTOL. In many cases, motors made with Hiperco® alloys can be up to 30% smaller.
- Low Coercivity: A magnetic material's coercivity refers to its resistance to demagnetization. Hiperco® alloys exhibit exceptionally low coercivity, which results in reduced energy losses during magnetization cycles. This characteristic is particularly beneficial in high-frequency applications or motors that undergo frequent speed changes, as it minimizes heat generation and improves overall efficiency.
These properties make Hiperco® ideal for stators and rotors in motors where efficiency and performance are paramount. Though, as suggested earlier, precise assembly and bonding techniques are essential to leverage these advantages to their fullest. Carpenter Electrification's expertise lies in developing and implementing these techniques to maximize the potential of Hiperco® materials.
Optimized Bonding and Assembly: Carpenter Electrification's Approach
Our advanced bonding techniques ensure precise tolerances and repeatability of stacks for superior stator and rotor performance, with key aspects including:
- Customized Lamination Design: Optimizing the geometry and thickness of Hiperco® laminations to balance magnetic performance with mechanical strength.
- Specialized Heat Treatment: Implementing precise thermal processing to enhance the magnetic properties of Hiperco® alloys without compromising their structural integrity.
- Advanced Bonding Techniques: Utilizing bonding methods that maintain the tight tolerances required for optimal magnetic circuit design while ensuring mechanical robustness.
- Comprehensive Testing and Validation: Employing rigorous testing protocols to verify both the magnetic and mechanical performance of assembled Hiperco® stator and rotor stacks.
The results of these optimized processes are significant and include the following:
- Reduced Mechanical Losses: Minimizing vibration and inefficiencies in high-performance applications.
- Enhanced Durability: Improving the longevity of motor components, particularly in demanding environments.
- Increased Power Density: Allowing for more compact motor designs without sacrificing performance — up to 30% greater power density.
Industry Benefits of Optimized Stator and Rotor Stacks
The advantages of our optimized stator and rotor stacks extend far beyond simple performance metrics. These advanced components offer a range of benefits that can transform the capabilities and economics of electric motors across multiple industries. Let's explore these benefits in detail:
Durability and Reduced Maintenance
- Longer Lifespan: Better bonding leads to more durable components, reducing the need for frequent replacements.
- Lower Operational Costs: Reduced downtime and fewer repairs result in substantial cost savings for operators.
Scalability and Customization
- Flexible Production: Our processes can be scaled to meet varying production volumes without compromising quality.
- Tailored Solutions: We work closely with clients to develop custom bonding solutions that suit unique motor designs and performance requirements.
Industry-Specific Benefits
Our optimized stator and rotor stacks offer unparalleled benefits across industries, including:
- Automotive (EVs) and Aerospace (eVTOL): Enabling more efficient, compact, and powerful electric drivetrains, which increase range and payload capacity, improve performance, and provide design flexibility.
- Renewable Energy: Enhancing the efficiency and reliability of generators in wind turbines and other renewable energy systems. This can increase energy output and reduce maintenance costs for renewable energy installations.
- High-Precision Manufacturing Equipment: Providing capability for high-speed positioning with excellent accuracy and repeatability. This is necessary for the equipment used to produce semiconductors and other advanced electronics.
How Carpenter Electrification Stands Out in the Market
Carpenter Electrification leads the electric motor industry with innovative technology, deep expertise, and a commitment to pushing the boundaries of motor design.Our unique position in the market is built on several key pillars, including:
- Unparalleled Material Knowledge: We deeply understand Hiperco® alloys and their optimal processing. Our team continuously refines material properties for specific applications, ensuring peak performance in every use case. We provide expert guidance on material selection and design considerations, helping our clients make informed decisions that maximize the potential of their motor designs.
- Cutting-Edge Technology: Our proprietary manufacturing processes and equipment set new industry standards. We employ advanced lamination stacking and bonding technologies that achieve unprecedented levels of precision and performance. Our state-of-the-art testing and quality control facilities ensure that every component meets the highest standards of excellence.
- Comprehensive Solutions: We offer end-to-end support from material selection to final assembly, providing a seamless experience for our clients. Our approach optimizes designs for performance and manufacturability, ensuring practical solutions that excel in real-world applications. We achieve seamless integration of material properties, stack assembly, and motor performance, resulting in superior end products.
- Customization and Flexibility: We develop tailored solutions to meet specific performance targets, understanding that each client's needs are unique. Our manufacturing capabilities scale seamlessly from prototypes to high-volume production, adapting to our clients' changing needs. We maintain ongoing partnerships for continuous improvement, ensuring our solutions evolve with our clients' requirements.
- Commitment to Sustainability: Our solutions enhance motor efficiency and reduce energy consumption, contributing to a more sustainable future. We actively research sustainable materials and processes, constantly seeking ways to minimize our environmental impact. Our technologies play a crucial role in enabling the growth of electrification and renewable energy systems.
- Collaborative Approach: We help our clients stay at the forefront of motor technology. We engage in joint development projects for cutting-edge applications, combining our expertise with our clients' innovative ideas. Our team provides responsive technical support throughout the product lifecycle, ensuring our clients' success at every stage.
We're not just providing components — we're delivering comprehensive solutions that enable our clients to push the boundaries of electric motor performance, efficiency, and reliability. As the demand for high-performance electric motors continues to grow across industries, our expertise and innovative approach position us as the ideal partner for manufacturers looking to gain a competitive edge in this rapidly evolving field.
The Bottom Line on Optimized Assembly and Bonding for Stators and Rotors
By now, the strategic advantages offered by Carpenter Electrification's optimized bonding and assembly processes for Hiperco® stators and rotors should be increasingly evident. Our advanced techniques push the boundaries of what's possible in motor performance and address critical industry challenges, providing a comprehensive solution that delivers tangible benefits across various applications. These benefits include:
- Higher motor efficiency, translating to energy savings and improved performance
- Enhanced durability, reducing maintenance costs and downtime
- Tailored solutions to fit diverse needs across different industries
- Reduced long-term operational costs through improved reliability and efficiency
As the demand for high-performance electric motors continues to grow across industries, the importance of precision in stator and rotor assembly cannot be overstated. Carpenter Electrification's advanced techniques and deep expertise in Hiperco® alloys position us as the ideal partner for manufacturers looking to push the boundaries of what's possible in electric motor technology.
Ready to take your motor manufacturing to the next level? Contact Carpenter Electrification today for a consultation and discover how our optimized assembly and bonding solutions can transform your products and give you a competitive edge in the market.