Complete Guide to Electric Motor Optimization: From Design to Testing
| 8 min read
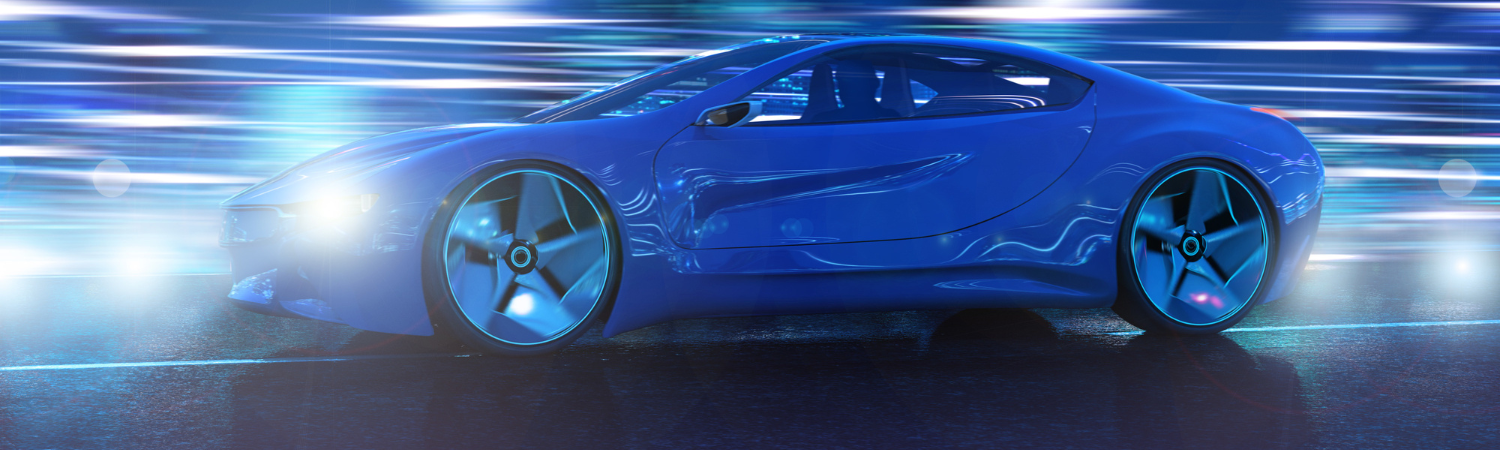
Electric motors power everything from our cars and appliances to factory machinery and aircraft. As industries increasingly shift toward electrification, understanding how to optimize these essential components becomes critical for engineers, designers, and decision-makers.
At Carpenter Electrification, we focus on developing cutting-edge solutions for motor optimization through advanced materials, rigorous testing, and innovative design approaches. This guide explores the intricacies of electric motor design, testing, and optimization, drawing from our extensive industry experience.
Overview of Electric Motor Components
An electric motor converts electrical energy into mechanical energy through magnetic field interactions. The process begins with the stator, a stationary outer shell housing a series of coils, which work in concert with the rotor, a rotating inner shell made up of a magnet, a series of magnets, or electromagnetic elements. When electric current flows through the stator coils, it creates a magnetic field that interacts with the rotor's magnetic field, generating rotational force or torque.
We've refined each component to maximize performance and efficiency. Our engineering teams have developed sophisticated manufacturing processes that enhance magnetic properties while ensuring consistent quality across production runs. Through extensive research and development, we've optimized each critical component to work harmoniously, creating motors that exceed traditional performance metrics.
These essential components work together in a precisely engineered system to power the electric motor. These include:
- Stator: Constructed from advanced soft magnetic alloys, it delivers superior magnetic permeability and minimal losses.
- Rotor: Incorporates permanent magnets or specialized soft magnetic materials for optimal magnetic field interaction.
- Stator Windings: Cooper conductors form the coil that carries electricity around the stator coil. The copper fill factor in the stator slots is an important performance factor.
- Precision Bearings: Bearings are used to support and guide the rotor and output shaft for smooth operation.
- Cooling Systems: Tailored to operating conditions to maintain optimal temperature profiles. It can be simple, like a fan, or complex, like a liquid cooling system.
Guide to Electric Motor Types and Enhancing Performance with Advanced Materials
Navigating Modern Motor Design Challenges
Today's electric motor designers face complex challenges beyond basic performance optimization. The increasing complexity of modern motors, with their higher power densities and tighter tolerances, has transformed motor design into a sophisticated optimization problem requiring advanced simulation tools and computational methods.
Managing Complexity Through Innovation
One of the most significant challenges lies in adopting new design methodologies and technologies. Organizations must cultivate a culture that encourages innovation while providing comprehensive training and support for new approaches. Agile methodologies and modern collaboration tools have become essential for streamlining design processes and adapting to evolving requirements.
The Critical Role of Compliance and Verification
As motors become more sophisticated, automated model verification has become increasingly crucial. Modern designs must comply with industry standards and regulations, necessitating rigorous verification processes that validate designs against predefined criteria. This systematic approach to verification not only ensures compliance but also maintains consistent quality across production runs.
Thermal Management: A Key to Reliability
The relationship between heat generation and motor performance cannot be overstated. Excessive heat can lead to catastrophic failures through insulation breakdown, wiring damage, and bearing wear. Successful thermal management requires a comprehensive approach that begins at the design phase and extends through material selection to cooling system implementation. Modern motors may employ anything from forced air systems to advanced liquid cooling solutions, depending on the application's specific requirements.
Material Selection for Optimal Performance
Material selection fundamentally shapes every aspect of electric motor performance, from efficiency and power density to longevity and reliability. Our research and development efforts have culminated in the creation of advanced soft magnetic alloys that significantly outperform traditional silicon steel in crucial performance metrics.
Our proprietary soft magnetic alloys and materials, including Hiperco50®, emerged from a deep understanding of the relationships between material microstructure, magnetic properties, and motor performance requirements. These advanced materials perform better through carefully engineered crystalline structures that minimize energy losses while maximizing magnetic flux density and permeability. The higher electrical conductivity reduces eddy current losses, allowing motors to operate at higher frequencies without sacrificing efficiency. When implemented in stator cores, these materials enable a 20-30% reduction in motor size while maintaining or improving power output — a critical advantage in applications where space and weight constraints pose significant design challenges.
Through extensive testing and real-world application, we have demonstrated several key performance advantages for high-performance motors:
- Up to 3% higher motor efficiency as compared to traditional
- Increased motor power density of 20 - 30%
- 15 - 25% higher torque density
The thermal characteristics of our soft magnetic alloys represent another significant advancement in motor material technology. Traditional materials often generate excessive heat during motor operation, forcing designers to implement aggressive cooling solutions or reduce power density. The heat generated increases with higher frequency, so it is a significant challenge in high-performance motor design.
Our advanced alloys and thin motor laminations have high efficiency, resulting in cooler operating temperatures that maintain consistent magnetic properties across a broader temperature range, allowing for more compact designs and simplified thermal management systems. This thermal stability in applications with high peak torque and continuous power requirements results in motors that maintain peak performance in applications with high peak torque and continuous power requirements.
Testing Methodologies: Ensuring Performance Under Real-World Conditions
Once materials are selected and designs are optimized, it's essential to validate the motor's performance through comprehensive stator testing. Traditional testing methods, such as ring testing at the lamination level, don't capture the full spectrum of real-world conditions. That's why Carpenter Electrification has developed a more advanced, multi-point magnetic response evaluation and dynamic testing protocols to ensure optimal motor performance.
Our testing approach includes the following:
- Core Loss Characterization: We measure energy losses at multiple frequencies and load conditions, ensuring minimal efficiency degradation across a wide range of operational scenarios.
- Thermal Behavior Mapping: We can refine cooling designs and prevent overheating in critical applications by simulating the motor's thermal response under varying conditions.
- Mechanical Integrity Testing: We subject components to vibration and resonance tests, simulating real-world stresses that could lead to motor failure. This is especially important in high-vibration environments like industrial machinery and aerospace applications.
These are further supported by additional testing, where we simulate prolonged use in harsh conditions, ensuring the motor performs reliably over its entire lifespan.
Maintaining Consistency Across Production with Quality Assurance
While testing ensures performance, quality assurance guarantees that every motor component meets strict standards throughout manufacturing. At Carpenter Electrification, we don't just rely on end-of-line testing but ensure consistency at every stage of production, from raw materials to final assembly.
Our quality control system uses advanced measurement technologies and predictive analytics to monitor every aspect of motor production. That includes the following:
- Material Properties: We verify the consistency of key materials, including magnetic permeability and thermal conductivity, ensuring that each batch meets the same high standards.
- Dimensional Accuracy: We employ precision measurement tools to ensure all components are fabricated to exact specifications.
- Assembly Integration: Every motor undergoes rigorous testing to confirm that components align correctly and maintain electrical integrity, which is critical for long-term reliability.
Additionally, we convert our data into meaningful and applicable formats for motor designers, evaluate data against industry benchmarks, and investigate any deviations to ensure quality in future endeavors. This proactive approach allows us to catch potential issues and rectify them, ensuring that the final product performs as intended and meets the high standards our customers expect.
The Carpenter Electrification Difference in High-Performance Solutions
Real-World Applications Across Industries
The practical application of our optimization strategies and advanced materials manifests across various industries. Each industry presents unique challenges, but our deep understanding of these diverse applications enables us to develop motors that meet and exceed specific performance requirements.
Here is a closer look at different use cases:
- Electric Vehicles: In automotive applications, especially EVs, optimizing power density and efficiency is crucial. By reducing motor size by up to 25% and increasing efficiency by up to 30%, we help manufacturers enhance vehicle range, reduce weight, and improve acceleration.
- Aerospace: We ensure reliability through extensive testing and performance via stator and rotor design and construction for electric vertical takeoff and landing (eVTOL) aircraft, where weight is critical. Our stacks also resist thermal cycling and vibrations, vital in aerospace environments.
- Industrial Applications: In manufacturing and heavy industry, our motors are designed for continuous operation under varying loads, with robust cooling systems and high starting torque to meet the demands of these environments.
- Household Appliances or Consumer Electronics: Many household appliances, such as washing machines and refrigerators, use electric motors to power various functions.
- Medical: Medical equipment applications such as Surgical Robots and Surgical Power Tools are increasingly turning to miniature motors that provide high power and that operate at high frequency with low loss.
- Defense: Legacy and new naval ships, aircraft, and land vehicles require small, lightweight and powerful motors and generators for peak operating performance.
Reach Out to Carpenter Electrification
Electric motor optimization represents a complex interplay of materials science, engineering precision, and rigorous testing methodologies. Our commitment extends beyond incremental improvements to fundamental innovations that reshape what's possible in electric motor design. We continue to establish new benchmarks for motor performance across diverse applications by strategically using advanced materials, sophisticated testing protocols, and comprehensive optimization strategies.
Contact Carpenter Electrification to explore how our advanced materials, testing capabilities, and optimization expertise can enhance your electric motor applications.