How Carpenter Electrification’s Strip Processing Solutions Are Powering Tomorrow’s Technology
| 7 min read
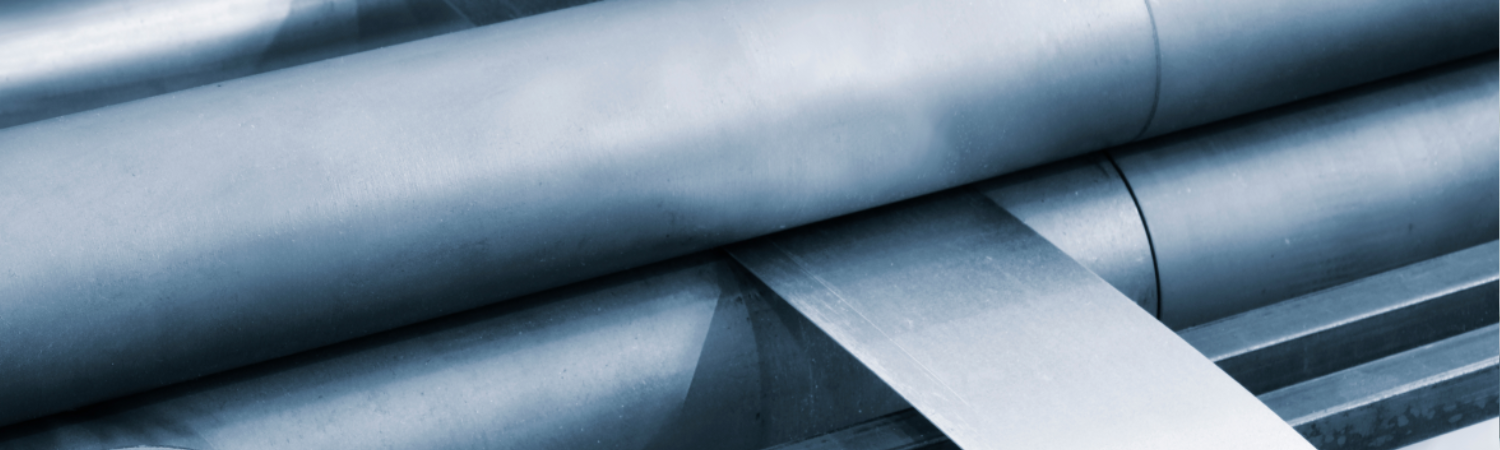
Strip processing technology is a cornerstone of modern manufacturing, driving innovation across industries from consumer electronics to vehicle and aircraft electrification. As engineers and designers push the boundaries of material performance, our team at Carpenter Electrification continues to pioneer advancements that meet these evolving demands. This post explores the cutting-edge developments in strip processing and their profound impact on the future of manufacturing.
What is Strip Processing?
Strip processing encompasses sophisticated techniques to transform metal alloys into thin, flat strips with precisely controlled dimensions and properties. This critical manufacturing process serves as the foundation for numerous industries, providing essential materials for applications ranging from electric vehicle motors to advanced power systems and aerospace components.
The strip processing journey typically involves several key stages, such as:
- Melting: Advanced techniques like vacuum induction melting (VIM) and vacuum arc remelting (VAR) are used to create high-purity alloys.
- Hot Rolling: Transforming ingots into thin strips using state-of-the-art rolling mills.
- Cold Rolling: Further refining the strip's thickness and properties.
- Finishing: Applying coatings, slitting, or other treatments to meet specific requirements.
The quality and characteristics of these strips directly influence end-product performance, efficiency, and reliability, making advancements in strip processing technology crucial for driving innovation across industries.
New Advancements in Strip Processing Technology
In recent years, we have witnessed remarkable progress in advanced, high-precision strip processing technology, with our team at Carpenter Electrification leading the charge. Some key advancements include:
- Precision Hot Rolling: Our new state-of-the-art hot rolling mill incorporates advanced automation and control systems, enabling unprecedented levels of precision and consistency. This mill can achieve tight thickness tolerances of ±0.001 inches and superior surface finishes, even at high production speeds.
- Advanced Melting Techniques: We've enhanced our VIM and VAR capabilities, allowing for the production of ultra-high purity alloys with exceptional mechanical and soft magnetic properties. Our largest VIM furnace can process enormous pounds of material per heat, ensuring consistent quality even for large production runs.
- Innovative Cold Rolling: Our cold rolling process now incorporates real-time thickness monitoring and adjustment, ensuring thickness variations as low as 0.0001 inches across the entire length of the strip.
- Cutting-Edge Finishing: We've implemented advanced coating technologies and precision slitting capabilities, allowing for customized surface treatments and tight-width tolerances.
- Integrated Process and Control: We provide end-to-end traceability and real-time process optimization, ensuring consistent quality from melt to finished product.
These advancements open up new possibilities for creating materials with tailored characteristics to meet specific application requirements, pushing the boundaries of what's possible in material science and engineering.
Key Benefits for Manufacturing Industries
The latest strip processing technologies offer a wealth of benefits to manufacturing industries, including:
- Enhanced Precision: Tighter tolerances and improved consistency lead to higher-quality end products. For example, in electric motor production, our precision-processed strips enable the creation of Hiperco® stator and rotor stacks with profile tolerances as low as 0.002 inches, significantly tighter than the industry standard of 0.006 - 0.008 inches, significantly improving motor efficiency and power density.
- Increased Efficiency: Our automated systems and optimized processes reduce production times by up to 50% compared to traditional methods while also minimizing material waste. This translates to faster time to market and improved cost-effectiveness for our clients.
- Material Innovation: Our advanced processing techniques enable the development of new alloys with superior properties. For instance, our latest generation of Hiperco® alloys offers higher magnetic saturation compared to conventional electrical steels, revolutionizing the design possibilities for high-performance electric motors.
- Scalability: Our modern equipment can handle both small-batch prototyping and high-volume production, facilitating faster product development cycles and seamless scaling from concept to mass production.
- Improved Sustainability: By optimizing material usage and reducing energy consumption in manufacturing, our advanced strip processing technologies contribute to more sustainable production practices, helping our clients meet increasingly stringent environmental regulations.
How Our Solutions Are Pioneering Innovation
At Carpenter Electrification, we're pushing the boundaries of what's possible in strip processing, particularly in the realm of soft magnetic alloys for electric motors and power systems. Our Hiperco® family of iron-cobalt alloys, combined with our advanced processing techniques and custom strip processing solutions, enables the production of motor components with exceptional magnetic properties.
For example, this translates to motors with higher power density, improved efficiency, and reduced size and weight for applications in eVTOLs, electric airplanes, defense, and precision manufacturing equipment. Specifically:
- Our Hiperco® 50 offers nearly 25% higher induction and 30% lower losses than conventional electrical steel and is available in thicknesses from 01. to 0.5mm. These results enable the creation of electric motors with improved power densities of up to 30% without sacrificing torque.
- Our tight thickness tolerances allow for the production of thinner laminations, reducing eddy current losses and improving overall motor efficiency.
- Our advanced stacking techniques, including our proprietary bonding process, result in stator and rotor stacks with improved mechanical stability and thermal performance, extending motor life and reliability.
These advancements directly address key challenges in EV design, such as extending range and increasing payload capacity.
Tailored Solutions for Industry-Specific Challenges
Our approach goes beyond simply providing high-quality materials. We offer comprehensive partnerships to ensure optimal performance and seamless integration of our products into clients' applications. For instance, we provide solutions for different industry obstacles, such as:
- Aerospace Sector: In an industry where stringent tolerances and reliability are paramount, our expertise in producing high-precision stator and rotor stacks enables the development of more efficient and lightweight electric propulsion systems for eVTOL aircraft. Our AS9100 certification and experience with FAA requirements ensure that our products meet the exacting standards of aerospace applications.
- Renewable Energy: For wind turbine generators, our advanced strip processing capabilities facilitate the production of high-performance materials that increase energy conversion efficiency compared to conventional materials. These seemingly small improvements can translate to significant increases in annual energy production for large-scale wind farms.
- Consumer Electronics: Our ability to produce ultra-thin strips with excellent magnetic properties enables the creation of smaller, more efficient sensors, audio drivers, transformers, and inductors for compact electronic devices. This capability has helped our clients reduce the size of power supply components while maintaining or improving performance.
- Medical Devices: In the medical power tools sector, our high-performance soft magnetic materials contribute to the development of more efficient surgical drills and bone saws. The exceptional magnetic properties of our materials allow for high RPM operation and smaller handheld equipment size, improving surgeon handling and patient outcomes.
Why Investing in Advanced Strip Processing Is Crucial for Future Growth
Investing in advanced strip processing technologies is about keeping pace with current industry standards and preparing for future demands and opportunities. Companies that embrace these innovations position themselves to:
- Accelerate product development cycles, bringing new designs to market faster. As noted, our prototyping and sampling capabilities can significantly reduce development time compared to traditional methods.
- Achieve higher performance metrics in their products, gaining a competitive advantage. For example, EV manufacturers using our advanced materials have reported range improvements thanks to increased motor efficiency.
- Reduce long-term costs through improved efficiency and reduced waste. Our clients have reported overall production cost reductions when factoring in improved yield, reduced scrap, and increased energy efficiency.
- Meet increasingly stringent regulatory requirements, particularly in industries like automotive and aerospace. Our materials and processes are designed to meet and exceed current and anticipated emissions, efficiency, and safety standards.
- Adapt more quickly to changing market demands and emerging technologies. The flexibility of our processing capabilities allows for rapid adaptation to new material requirements, ensuring our clients stay at the forefront of their industries.
Connect With an Expert Today
The advancements in strip processing represent a significant leap forward in manufacturing capabilities, offering unprecedented opportunities for innovation and growth across multiple industries. As we continue to push the boundaries of what's possible in electrification, the role of high-performance materials and precision processing becomes ever more critical.
For companies looking to stay ahead of the curve and drive innovation in their respective fields, it's time to explore these advanced strip processing solutions and unlock new possibilities. Reach out to our team of experts to discuss how our cutting-edge technologies and customized approach can help propel your products — and your business — into the future.