Thermal Management Solutions for High-Performance Electric Motors
| 5 min read
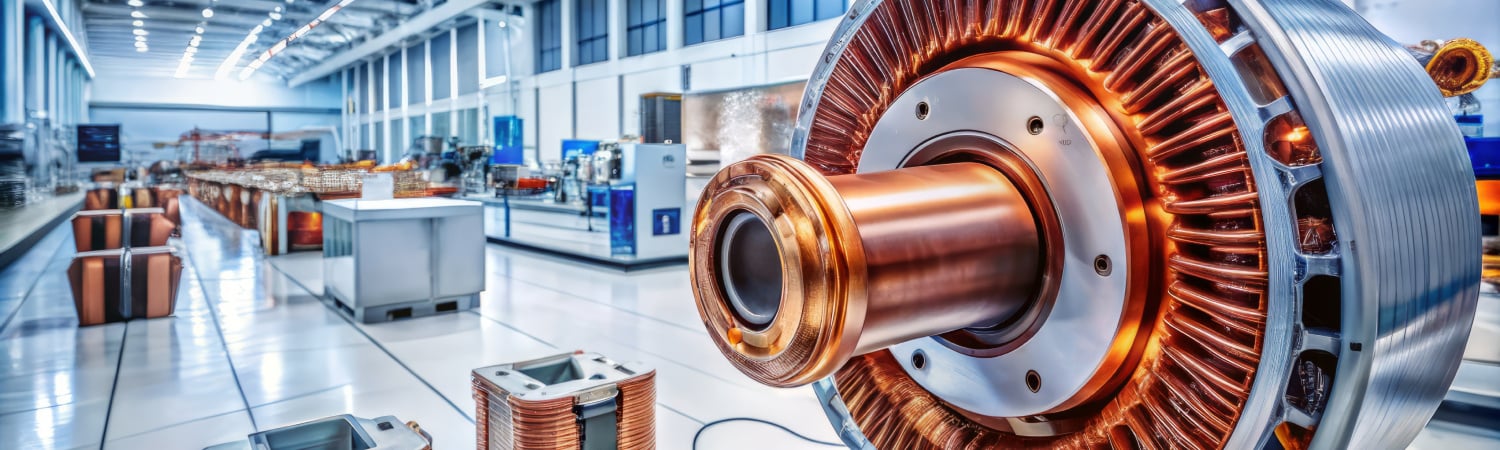
The high-performance electric powertrains in eVTOL air taxis, electric and hybrid-electric aircraft, and electric vehicles require advanced thermal management solutions. While each of the primary powertrain components – batteries, inverters, and electric motors – present unique challenges, two basic thermal management principles are true for all three: minimize heat generated within the component and efficiently remove any heat that is generated. OEMs and component suppliers are turning to advanced materials and novel designs to improve performance.
The relentless drive toward higher power density in electric motors creates unprecedented thermal management challenges. As power density increases, the heat generated within compact motor designs intensifies, demanding innovative cooling solutions that extend beyond traditional methods. At Carpenter Electrification, our deep expertise in electric motor materials allows us to tackle these thermal challenges head-on. Let's explore more.
Understanding Heat Generation in Modern Electric Motors
Electric motor efficiency has reached remarkable levels, yet energy losses persist. These losses manifest primarily as heat in the stator windings, lamination stacks, and bearings. A 50 kW motor operating at 95% efficiency still generates 2.5 kW heat — equivalent to two household heaters running at full power. This heat, concentrated in a compact space, must be managed effectively to prevent performance degradation and potential failure.
Eddy current losses in lamination stacks are a significant contributor to total heat generation, particularly at high frequencies common in aerospace, EV, and medical applications. At operating frequencies above 400 Hz, these losses can constitute 10% to 30% of total motor losses, depending on lamination thickness, material selection, and insulation quality. The relationship between frequency and core losses is non-linear, with eddy current losses increasing quadratically and hysteresis losses increasing linearly as frequency rises. This presents significant challenges in high-speed motors, where operating frequencies can exceed 1000 Hz, leading to increased heating and material constraints.
Material Selection: The Foundation of Thermal Management
The choice of materials profoundly impacts a motor's thermal performance. Our Hiperco® iron-cobalt alloy family, renowned for its magnetic properties, also plays a crucial role in thermal management. These advanced materials exhibit higher thermal conductivity than conventional electrical steels, facilitating more efficient heat transfer from the motor core.
Lamination thickness proves critical in managing eddy current losses. Our ultra-thin Hiperco® 50 laminations, available down to 0.1mm thickness, significantly reduce eddy current losses — potentially by more than 70% compared to traditional 0.35mm laminations—depending on operating conditions. This reduction in core losses directly translates to lower heat generation and improved motor efficiency. Combined with our precision stacking techniques, these thin laminations maintain their superior magnetic properties while providing enhanced thermal performance.
Learn More About Lamination Thickness: Hiperco® 50 Datasheet
Advanced Cooling Strategies for Modern Motors
Today's high-performance powertrains utilize multiple cooling methods, sometimes working in concert. System engineers can choose between air-cooled or liquid-cooled approaches for the electric motor. Air-cooled designs incorporate fins or similar features to increase surface area and improve heat transfer as air flows across the motor. This simpler approach reduces cost, weight, and maintenance. However, the heat removal performance does not match liquid-cooled systems.
Direct liquid cooling, facilitated by precisely engineered channels in the motor housing, serves as a more efficient primary heat removal mechanism. These channels, optimized through computational fluid dynamics (CFD) analysis, typically maintain a coolant flow rate of 10-15 liters per minute, removing 60-85% of the generated heat, depending on design parameters. Additional cooling occurs through oil-spray systems, which target high-heat regions, particularly the end windings and bearings, where traditional cooling methods are less effective.
Thermal interface materials (TIMs) are crucial in enhancing heat transfer between motor components. Advanced ceramic-filled polymer TIMs achieve thermal conductivity values exceeding 5 W/mK, significantly reducing thermal resistance at critical interfaces. Proper selection and application are essential, considering operating temperature, mechanical pressure distribution, curing behavior, and long-term stability to ensure optimal thermal performance and reliability.
Industry-Specific Solutions
Different applications demand tailored thermal management approaches. In aerospace applications, where weight is paramount, lightweight cooling solutions such as integrated heat pipes and phase-change materials (PCMs) within composite airframes have been developed. For example, electric propulsion systems for aircraft from companies like ZeroAvia and MagniX rely on advanced liquid cooling to maintain efficiency while minimizing added weight. Similarly, thermal management in satellite electric propulsion systems, such as those used in SpaceX's Starlink satellites, employs radiation-based cooling and heat spreaders to dissipate excess heat in a vacuum environment.
In high-performance electric vehicles (EVs), direct cooling of stator windings, as seen in some high-end models, enables sustained high power output by reducing thermal limitations. Formula E race cars utilize dielectric fluid cooling for inverters and electric motors, enhancing heat dissipation while maintaining compact, lightweight designs. Thermal management systems integrate with vehicle-level cooling circuits, optimizing overall system efficiency while handling peak loads during acceleration and regenerative braking.
Watch Our Latest Webinar: Exploring the Future of Electrification
Manufacturing Considerations
The implementation of these advanced cooling architectures requires new considerations for the manufacturing of systems and components. The considerations of the stators and rotors in advanced motors go beyond incorporating advanced materials like TIMs and iron-cobalt alloys. Cooling requirements have led to novel features and greater complexity in stator and rotor designs. Air-cooled motors often have fins or non-round surfaces on the outer diameter.
These features make grinding either impractical or impossible. The interior fluid channels on liquid-cooled stators require accurate layer-to-layer registration of the laminations. Consistent adhesive dispersion and complete coverage between laminations are also critical to maintaining desired fluid flow characteristics and avoiding leaks within the stator. We see increasingly complex stator and rotor constructions incorporating multiple lamination designs within a single stack. These trends require more stringent dimensional tolerances to achieve the necessary stack quality.
Reach Out to Connect with Our Team
At Carpenter Electrification, our technology development and stack production efforts focus on integrating these innovations into practical, scalable solutions that advance the state of the art in motor thermal management. Contact our team to explore how our thermal management expertise can enhance your motor design. We partner with you to optimize electric motor performance from material selection to stator and rotor prototyping to high-volume scale-up of stack production.